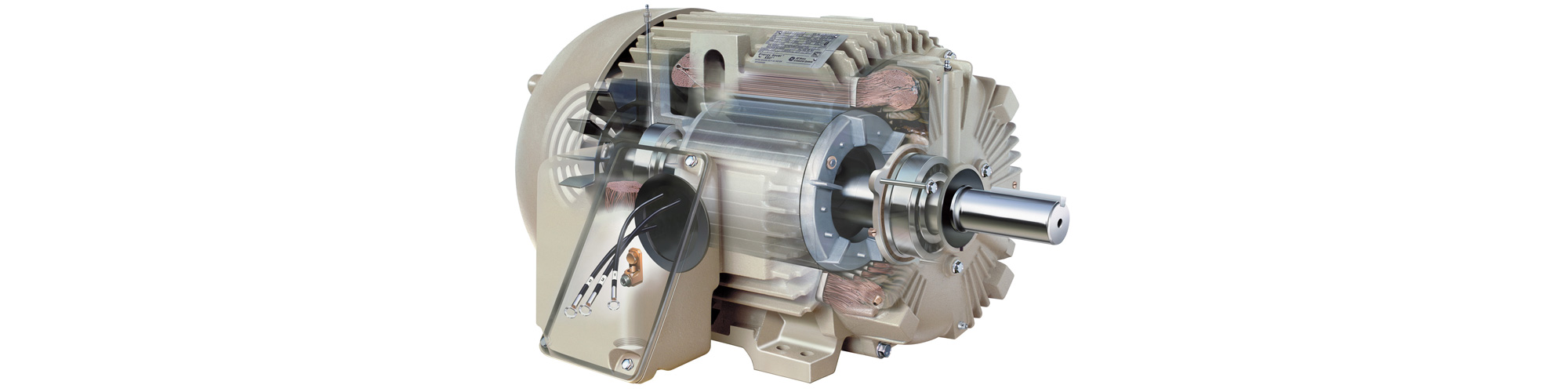
Motors Are Our Specialty
Located in Dayton, Ohio, M & R Electric Motor Service Inc. is your source for electric motor repair. We specialize in both residential and commercial motors. Our knowledgeable staff can sell you a new motor from our selection of products or perform a full motor repair including installing new bearings, fixing damaged housings and shafts, rewind service, or performing a core loss tests in the worst situations to see if you should repair your motor. Other specialties include:
- Premium Efficiency Motors
- AC Inverter Drives & Motors
- DC Servo Motors
- Electromagnetic Chucks
- Farm Duty Motors
- Gates Belts
- Laser Alignment
- Material Hand Motors
- Motor Balancing
- Motor Bases
- Phase Converters
- Pump Repair
- Rewind Services
- Starters & Contactors
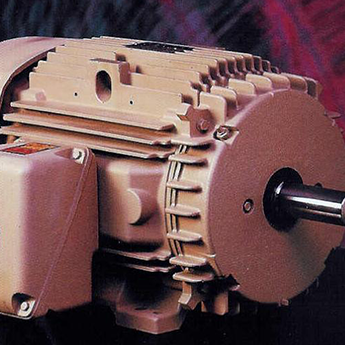
Diagnose & Repair Motor Failures
When you are experiencing motor failure and are unsure about how to proceed, let us try to help before you even give us a call. Consult the chart below to easily diagnose many of the most common motor issues and find out how to move forward.
Failure | Probable Cause | Corrective Measures |
---|---|---|
Motor Fails to Start |
|
|
High Noise Level |
|
|
Overheating of Bearings |
|
|
Intense Bearing Vibration |
|
|
Overheating of Motor |
|
|